Blow Air In, Not Out
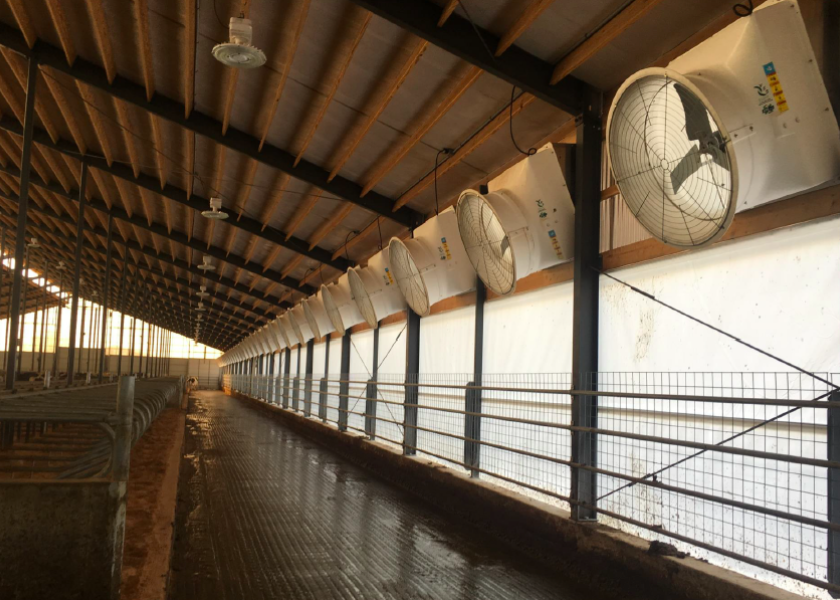
Exhaust fans were always just that—blowing air out of buildings to expel stale air and draw fresh air in.
But a unique barn design, developed by Gordie Jones, a Wisconsin veterinarian and dairy consultant, turns that conventional wisdom on its head. The new design uses fans along both lengths of curtain-sided dairy barns to push fresh air into the buildings and vent exhaust air up through a center ridge.
The concept allows the barns to naturally ventilate when temperatures are moderate—typically 70% of the time in Midwest. The sidewall fans are only used for summer-time ventilation when the temperature-humidity index (THI) reaches 68°F to provide 40 to 60 air exchanges per hour.
In winter, sidewall curtains and a curtain on the roof’s overshot ridge are regulated to provide four continuous air exchanges per hour when temperatures drop to 10 to 15°F. Large, high-volume, low velocity fans spaced over the feed lane push warm air back down to aid in warming the building at cow level.
The goals of this design is three-fold, says Jones:
•To allow natural ventilation to occur most days of the year.
•To provide consistent air flow, and no dead spots or bunching of cows, through the entire building when heat stress occurs.
•To prevent manure from freezing to alleyways in winter.
“This design can achieve those goals,” says Jones.
The problem with conventional curtain-sided buildings is they typically can’t provide enough cooling air flow in summer when temperatures soar and the wind stops blowing. Fans with sprinklers over feed lanes and fans alone over freestall beds can help, but they typically don’t provide enough air exchanges to mitigate heat stress.
In winter, dairy farmers typically button up the buildings as tight as they can to avoid manure from freezing. But that can shut down any ventilation, resulting in stale, foggy and steamy air remaining in the barns and creating conditions ripe for pneumonia.
Tunnel-ventilated and cross-vent barns were designed to reduce those problems. But they require at least some fans to run 100% of the time year-round. Cows furthest from the inlet side of these buildings continually breathe in the humid, bacteria-laden air from other cattle closer to the inlets. Any air penetration—opening doors to allow in feed trucks, bedding wagons or manure handling—also disrupts air flow and ventilation patterns. And large-scale, industrial back-up generators are required to ensure electrical power is always available.
Jones’ concept is, what he calls an “all-season, hybrid barn,” uses positive ventilation when it is needed to boost air flow in a naturally-ventilated barn. The size of fans is dictated by the width and volume of buildings. In a four-row barn, 3’ fans are used and positioned above curtains that run the lengths of both sides of the building. Sidewalls are 16’ in height to accommodate the fans and sufficient curtain openings.
Fans are positioned every 10’ so every four cows have access to a fan. Fans are tilted down to provide air flow over the freestall beds. Rather than a center ridge, the roof is overshot to create a larger opening for air to exhaust. (For the concept to work, the air outlet area must be equal to the air inlet area for peak, summertime ventilation.) A curtain on the center ridge regulates air exhaust in winter to keep too much heat from escaping while still providing four air exchanges per hour.
Large, 16’ high-volume, low velocity horizontal fans are also positioned every 80’ over the length of the feed lane to push air back down when power ventilation is needed. In summer, these fans create air turbulence at cow level to provide more effective cooling. In winter, they push warm air back down to the floor to help prevent manure from freezing. The roof is also insulated to reduce heat load in the building in summer and reduce condensation in winter.
First of Its Kind
Hank Wagner milks 650 cows with his wife, Pam, son, Shawn, daughter, Laura Raatz, and son-in-law, Tyler Raatz and six employees, near Oconto Falls in northeast Wisconsin. Their 25-year old facilities needed an upgrade.
“We’ve been in naturally ventilated barns since 1992. But we’ve been frustrated with heat stress and bunching in the barns,” he says. “We had fans over the stalls and feed lanes, but it wasn’t enough.
“We looked into power ventilation, and Gordie, who I’ve been a close friend of for years, brought his hybrid concept to us,” Wagner says.
That was in 2017. The problem: No one had built such a hybrid barn before. So Wagner and Jones spent that summer experimenting with different fans, sizes and positions to see what might work.
Wagner then built a new, 4-row barn with 258 stalls. It has 16’ sidewalls, an over-shot ridge opening and an insulated roof. The barn houses two groups of older cows—the Wagners’ second lactation cows and third and older lactation cows.
They have now gone through a year and half in the new barn, and it is performing as advertised. “We had an extremely hot summer this past summer and an extremely cold winter this year,” says Wagner.
“I’ve been charting milk production for the past 30 years. During our hot summer last year, we had zero milk production drop, zero signs of heat stress and no bunching,” he says. “One of the first signs of heat stress is more cows standing, and we didn’t see that at all last summer.”
The power ventilation of the building is governed by air temperature. No fans come on until ambient air temperatures reach 64°F. At 64°F, every third fan kicks on. At 68°F, another third of the fans start, and at 72°F, all fans run. All the fans are 3’ in diameter and are powered by ½ horsepower motors.
The fans are angled down 22°to provide air movement over the head-to-head freestalls. “We want the most comfortable spot in the barn be the beds,” says Wagner. Soakers (but no fans) are also used over the feed lane.
The new barn also performed very well this winter, when temperatures dropped to a bone-numbing
-35°F with no manure freezing. Note: Wagners milk 3X, so floors are scraped each time cows leave the pen for milking.
The Wagners have also retrofitted a couple of older, naturally-ventilated barns. These were a bit trickier to remodel since they only had 12’ sidewalls and an open ridge. An over-shot roof also had to be created, roof steel removed and insulation with new roof steel installed. These barns are also performing well.
Wagner acknowledges the hybrid barn design will cost a little more to build than a conventional, naturally ventilated barn because they require more sidewall height, fans, wiring, and controls. “But up to 64°F, we have no fans running at all. If we had had gone to complete power ventilation, we’d have some fans always running. With this concept, we have eight months of the year with no operating cost to the ventilation system,” he says.
Analysis by the University of Wisconsin shows annual power usage is about the same as a conventional, naturally-ventilated barn with fans over the feed lane and freestall beds.
Jones estimates 4-row hybrid barns can be built for about $3,200 per freestall bed. It’s a price, he says, that is well worth the investment because facilities last a long, long time. “Facilities are tools that let you implement your plan. If you don’t have a plan, the facilities will dictate your plan,” he says.